Giltron Inc. has decades of experience in all typical induction heating applications, including:
Joining. Induction systems for joining are readily automated, can incorporate precise temperature control. Induction joining offers superior speed and repeatability.
- Soldering
- Brazing
- Shrink Fitting
- Plastic to metal
- Glass to metal
- Plastic to plastic
- Plastic to foil
- Curing adhesives and epoxies
Heat Treating. Induction heat treating processes can offer automated cells, can be very fast, with no idling. and is also able to be precisely localized. Automation can allow hardening and tempering without moving the part.
- Deep hardening
- Surface hardening
- Tempering
- Annealing
- Stress relieving
Other induction applications that Giltron Inc. can assist with include:
- Catheter tipping
- Plastic forming
- Curing of coatings
- Fatigue testing
- Melting
- Crystal growing
- Zone refining
- Alloying
- Drying ink
- Levitation
- Warm forming
- Forging
- Glass melting
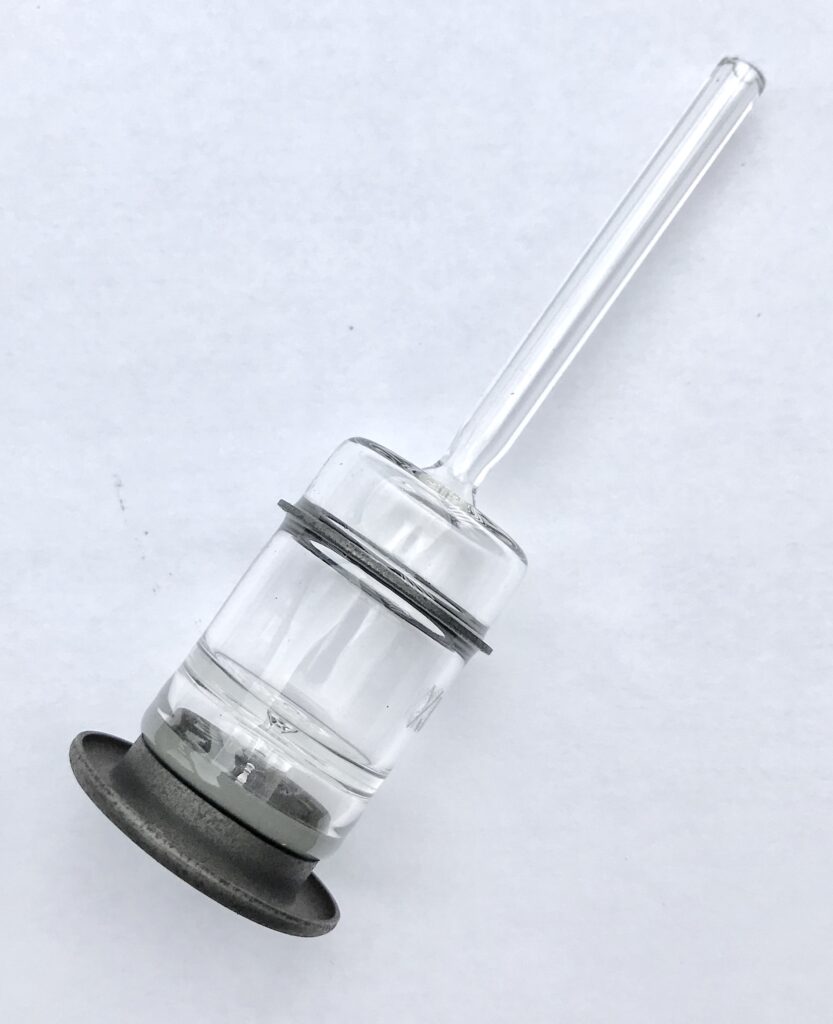
Process Control Capability
Induction heating provides significantly more process control than many other heating methods. Induction is also fast, and easy to automate and monitor. Induction often increases efficiencies.
Time control: Modern power supplies use digital or computer timers with .001 second repeatability.
Power control: Today’s generators feature regulated outputs often with power, voltage and current regulation options.
Temperature Control: Infrared optical pyrometers can provide highly accurate measurement and control.
PLC Control: Most units feature a central interface for process control signals (including on/off and power level) and feedback.
Speed control: Interfaces are available to modulate power output proportionally with line speed.
Giltron can design and build custom machines and control systems to automate or semi-automate your production, lowering unit costs and increasing yields.